Guidelines To Install Plumbing In A Detached Garage: Step-By-Step
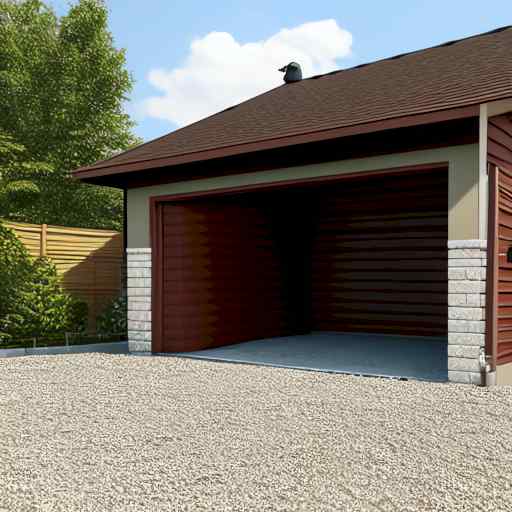
Introduction
The Importance of Plumbing in a Detached Garage
A detached garage is more than just a storage space for vehicles; it's an extension of the home that serves multiple purposes. Often used as a workshop, hobby area, or home gym, these multifunctional spaces can significantly benefit from having a dedicated plumbing system.
The presence of running water increases functionality, convenience, and even adds value to the property. Adding plumbing to your garage can transform it into an independent living area or guest house.
It allows for the installation of essential amenities like sinks, toilets, or even a full kitchenette if desired. You could rinse off garden tools without traipsing through your home with muddy shoes or have a convenient spot to wash your hands after working on your vehicle.
Moreover, having an accessible water source in your detached garage contributes to enhanced safety measures. A plumbed garage ensures that you have immediate access to water in case of fire emergencies - an important aspect often overlooked by homeowners.
Factors To Consider Before Installing Plumbing
Prior to embarking on the journey of installing plumbing in your detached garage, there are several crucial factors you need to contemplate on initial stages. First and foremost is understanding local building codes and regulations related to plumbing installation. Some jurisdictions may require obtaining permits before proceeding with any type of construction work which includes altering existing plumbing systems.
You also need to explore different types of plumbing systems and their suitability according to your specific needs and intended usage for the detached garage space. Are you simply planning for cold water supply or do you need hot water as well?
Are there going to be fixtures requiring drainage? These are important questions that will help guide you towards the right type of system.
The distance between your main house and detached garage is another factor worth considering as this will affect how much piping material will be needed and impact overall cost. Also consider possible challenges such as soil type and existing underground utilities which might require special care during excavation process.
Understanding Plumbing Basics
A Primer on Basic Plumbing Concepts
To embark on the journey of installing plumbing in your detached garage, a foundational grasp of plumbing principles is indispensable. Fundamentally, a plumbing system consists of two primary segments: the water supply system and the drainage system. The water supply system, as the name suggests, brings fresh water into your garage from the public water supply or private well.
This system operates under pressure to enable the flow of water upstairs and against gravity. On the other side of this aquatic coin lies the drainage or DWV (drain-waste-vent) system.
This silent hero expels waste and used water out from your garage into either a septic tank or sewer line. It relies on strategic angling and gravity to transport waste material downwards.
Vent pipes play a crucial role in this subsystem by replacing drained air that allows wastewater to flow freely. It's important to understand that each fixture in your garage will require both components of this plumbing dichotomy - namely an inlet for fresh water and an outlet for waste disposal.
The Imperative Nature of Building Codes & Permits
Before you commence any significant construction project like installing plumbing lines to your detached garage, it's paramount that you become familiar with local building codes and secure all requisite permits. Building codes are essentially safety standards set forth by municipal bodies designed to ensure structural soundness, fire resistance, adequate ventilation, hygiene standards etc., across all types of edifices.
In terms of plumbing specifically, these codes regulate everything from pipe material usage to their depth beneath ground level right down to appropriate fixtures installations. Noncompliance can result in hefty penalties and necessitate redoing laborious work - an expensive predicament best avoided through due diligence.
Moreover, obtaining necessary permits is not just legally mandated but serves as an extra layer of protection for homeowners too. It ensures that all work carried out aligns with professional safety standards and often involves inspections during different stages which further safeguards your investment.
Essential Tools & Materials Required For The Job
Installing new plumbing lines calls for not just technical knowledge but also certain specialized tools and materials which aid in carrying out this task proficiently: 1.Piping Material: Depending upon local building code regulations as well as personal preferences concerning durability vs price point trade-offs - options range from PVC (Polyvinyl Chloride), PEX (Cross-linked Polyethylene), Copper etc., 2.Measuring Tape & Marker: These are vital tools used frequently throughout every stage - be it while planning pipe routes or marking cut points during installation,
3.Pipe Cutter or Saw: These are needed for cutting pipes according to required length, 4.Soldering Torch & Flux (for copper pipes): This is used for securing joints ensuring they are watertight,
5.Wrenches & Pliers: These hand tools are used extensively during assembly, 6.Trencher (optional): Depending upon if excavation is needed and its scale - manual digging might suffice else renting machinery could save substantial time,
7.Protective Gear: Safety goggles & gloves safeguard against potential threats like flying debris during pipe cutting/soldering. A successful job marrying impeccable functionality with longevity boils down essentially to meticulous preparation married with principled execution.
Site Assessment and Planning
Evaluating the Site for Potential Challenges
The commencement of any successful plumbing project lies in the thorough evaluation of the site for potential challenges. The most crucial factors to consider include distance, soil type, and pre-existing structures.
For instance, a larger distance between your main house and detached garage may necessitate more materials and labor, consequently escalating the overall cost of installation. It's vital to scrutinize the soil type as well.
Sandy soils are easier to dig while clay soils might prove strenuous but provide a more stable environment for the pipes. Rocky terrains could pose significant difficulties in excavation, thus demanding specialized equipment or alternative routing.
Existing structures such as gas lines, utility conduits or sprinkler systems can also impact your plumbing route. It's essential to identify these before digging begins to avoid possible damage that might result in expensive repairs or dangerous incidents.
Determining the Best Route for Pipes from Main House to Garage
An effective pipeline route should minimize disturbance to landscape features while cutting costs on labor and materials. This process warrants a keen balance between pragmatism and compliance with local building codes.
In some instances, this might mean following a longer path around landscaping or structures rather than taking a direct route that would involve unnecessary complexity or cost. The chosen route must consider factors such as depth requirements--typically below frost line--to prevent freezing during winter months; it should also avoid areas with high vehicular traffic which could put pressure on pipes causing potential damage over time.
An efficient method of determining an optimal pipeline path is through creating a scaled drawing of your property indicating your home, garage, existing utilities, obstacles like trees or other buildings as well as potential paths for new pipes. This visual tool can greatly assist you in finding an ideal course for your piping system.
Deciding on The Type Of Plumbing System Suitable For Your Garage
Your planned use for the garage dictates which type of plumbing system you choose: cold water only; hot and cold water; drainage system--or all three combined if you foresee adding amenities like bathroom facilities or sinks in future. If only basic utility needs are required like garden hose connections or outdoor cleaning stations then opting for cold water supply alone is sufficient whereas any function needing warm water will require both hot and cold supply lines installed--one carrying hot water from your home's heater and another delivering cold water directly from your main line.
A comprehensive plan encompassing future upgrades can save you time-consuming modifications later on even if initial costs are higher. Therefore assessing current needs alongside future aspirations is crucial when deciding upon an appropriate plumbing system for your detached garage.
Designing Your Garage Plumbing System
The Blueprint of Pipe Sizes, Types and Locations
The creation of a comprehensive plan for your garage plumbing system is pivotal in ensuring its reliability. This plan should comprise the pipe sizes, types, and their precise locations. The diameter of your pipes is contingent on what they will transport.
Commonly, 1/2 inch pipes are sufficient for most fixtures except for the main water supply line which requires a larger diameter - usually 3/4 inch to ensure adequate flow. In reference to pipe types, three options take precedence -- PVC, PEX and copper.
PVC pipes are cost-effective and easy to work with but have a susceptibility to warping when exposed to hot water. Copper pipes are exceedingly durable but they can corrode over time and require soldering during installation -- a skill that could be beyond the ken of many home handymen.
PEX (cross-linked polyethylene) strikes an appealing balance between cost-effectiveness and durability. It can withstand both hot and cold water making it adaptable for diverse uses.
Accurately marking where each pipe goes is another vital aspect of your planning stage. This map should feature clear annotations denoting the path of each pipe from its source all through to its termination point.
Anticipating Future Needs
When designing your garage plumbing system, it's wise not only to focus on immediate needs but also consider future plans you may have for your space like adding a bathroom or kitchenette in the future. The inclusion of extra cold water lines while laying out your primary plumbing gives room for easy addition of these facilities down the line; it's more economical than having plumbers come back later on to do so retroactively which would involve excavating already finished areas causing unnecessary disruptions.
Additionally, if you anticipate needing hot water in these rooms later on, plan ahead by installing both hot and cold supply lines from the outset - even if you cap them off temporarily till they're needed. Another prudent action would be situating drain lines strategically under the slab -- again capped until required but present nonetheless so installing sinks or toilets becomes less laborious down the line.
Incorporation of Shut-Off Valves
Every well-designed plumbing system features shut-off valves at strategic points enabling homeowners to isolate certain parts without disrupting service elsewhere in case routine maintenance or unexpected leaks occur. To achieve this utility setup one needs two kinds: fixture shut-off valves situated right before every fixture (sink faucets et al.), and main shut-off valve placed where the supply line enters the building from outdoors allowing complete haltage if need arises. Having these valves within easy reach makes annual checks easier facilitating early detection if they're faulty negating potential catastrophic failures that could lead expensive repairs.
The Art of Earth: The Excavation Process
The first step in the excavation process is diagramming your property to identify existing utilities such as gas, electric, and sewer lines. This is crucial to avoid damaging them during the digging process.
Moreover, it is paramount that you are aware of their locations prior to excavating. You can do this through utility locating services or by obtaining blueprints for the property.
In addition to avoiding existing utilities, it's also important to consider other elements like tree roots or structures that could obstruct your trench. It may be necessary to alter your planned path slightly if you encounter these obstacles.
Also bear in mind that safety should always be a top priority during excavation - use appropriate personal protective equipment and never work alone. When excavating, remember that patience is key.
Rushing through this process can lead to errors which may be costly down the line. Take care not only while digging but also in creating clear, stable walls for your trench so as not to compromise its structure.
Unearthing Safety: Procedures on How To Dig Trenches Safely Without Damaging Existing Utilities
Before breaking ground with your shovel or mini-excavator, make sure you've clearly marked the location of all utilities based on your earlier diagramming or blueprint review. If you're unsure about any lines' location despite these measures, hand dig around those areas with a small shovel until they are located. In cases where heavy machinery like a mini-excavator is being employed for digging trenches, ensure there's always a spotter present whose sole responsibility is watching out for any signs of utility lines or potential hazards while the machine operator focuses on digging.
This simple yet effective system helps prevent accidental damage from occurring. Another aspect worth mentioning here pertains to how filled-in soil should be handled post-digging; pile it away from the edge of the trench so as not risk undermining its structural integrity by adding unneeded pressure on its sides.
Diving Deep: Detail On Depth Requirements Based On Local Codes
The depth at which you need to bury water supply and drain lines varies depending on local regulations and climate conditions; hence consulting with local building codes beforehand will equip you with necessary guidance regarding this critical aspect. Frost line (the maximum depth where ground freezes in winter) plays an influential role in determining pipe depth - typically pipes are placed 12 inches below this line to protect them from freezing temperatures which could potentially cause damage due piping expansion and contraction under extreme cold conditions . Certain zones might also require specific depths when installing drain-lines due gravity-based flow requirements; hence understanding these nuances become imperative before embarking upon such undertakings ensuring smoother execution while adherence regulatory stipulations.
Installing Water Supply Lines
A Perspicuous Examination of Pipe Types
When embarking on the task of installing water supply lines, it is crucial to consider the type of piping that will best suit your needs. The three most common types are PVC, PEX, and copper.
Polyvinyl Chloride (PVC) pipes are known for their affordability and ease of use. These lightweight, durable pipes can withstand high water pressure making them a popular option for main water lines.
However, one must bear in mind that PVC pipes are susceptible to becoming brittle over time when exposed to sunlight or freezing temperatures. Cross-Linked Polyethylene (PEX) pipes, on the other hand, are highly flexible and resistant to both extreme temperatures and corrosion.
While slightly more expensive than PVC pipe, PEX is easy to install and requires fewer connections which reduces the risk of leaks. Copper pipe holds a longstanding reputation for reliability in residential plumbing systems.
Renowned for its durability, resistance to corrosion and heat conductivity; copper remains an excellent choice albeit being more costly than its counterparts. Notwithstanding its material cost, the labor-intensive installation process due to soldering requirements might affect your final decision.
Connecting New Water Lines: A Detailed Procedure
Having chosen the appropriate piping material for your detached garage plumbing project, you will now venture into connecting these new lines with your existing home plumbing system. The first step involves closing down your home's main shut-off valve before you proceed with any connection or modification process.
This step is essential in preventing any unexpected gushes from open pipelines during the connection process. Secondly, identify an optimal location to tap into by studying your home's existing plumbing layout meticulously.
You must ensure that this location provides sufficient water flow without causing undue strain on your overall system. Once identified this optimal tap-in point; cut into it using a suitable tool such as a pipe cutter or hacksaw depending on whether you're dealing with metal or plastic pipes respectively.
Be sure to leave enough room on either side of this cut section for adding T-fitting which will serve as connection point for new line leading towards detached garage Next comes the installation of a T-fitting at this cut-off point using either push-fit fittings or soldering techniques based on selected pipe type; thereby giving rise to an additional branch from main water line heading towards our end destination - detached garage
But equally important is testing newly installed line post completion all connecting tasks by reopening main shut-off valve carefully while monitoring closely potential leakages along new line section as well at T-joint area Bear in mind though it may feel daunting initially; taking time understand each step across entire process can lead successful execution providing much-needed water supply detached garage
Unraveling the Intricacies of Installing a Drainage System
The Dichotomy Between Gravity-Fed Drain and Pump-Assisted Drain Systems
In the realm of drainage systems, there are primarily two contenders dominating the scene: gravity-fed and pump-assisted drains. A gravity-fed drain system, as its nomenclature suggests, relies on simple gravitational pull for its operation. Once water is introduced into the system, it naturally descends due to gravitational forces, resulting in an automatic clearing of wastewater from your garage.
However, this type of system requires careful planning because it necessitates a certain slope to facilitate effective drainage. Building codes generally prescribe that for every foot traveled horizontally by your drainpipe, there should be a vertical drop of 1/4 inch (a 2% slope).
Thus, if your terrain doesn't allow such inclination or if the garage is located uphill from your sewer line connection point at home, installing a gravity-fed drain can pose significant challenges. Conversely, pump-assisted drains are independent systems facilitated by technology.
They do not rely on slopes or gravity; rather they utilize electric pumps which forcibly transport wastewater from one location to another - overcoming height differences and horizontal distances with ease. This type is more versatile but requires regular maintenance to ensure optimal functioning of the pump.
Finding Harmony: Connecting Your Garage Drains to Your Home's Main Sewer Line
The process of harmonizing your new garage drain with your main sewer line may seem daunting at first glance; however, with meticulous planning and execution it can be achieved without undue complications. Before proceeding with this task though, it's crucial to acquire any necessary permits required by local building regulations. The first step in this endeavor involves mapping out where you will connect to the existing sewer line in accordance with local code regulations.
This typically means maintaining a minimum distance between potable water lines and sewer pipes for health safety reasons. Once you have established this connection point accurately on your layout map or planogram (which ideally should have been drafted during project planning), you can proceed with creating an interconnection channel.
This usually involves digging down until you expose part of the existing sewer pipe then connecting the new pipeline using suitable fittings like wyes or tees along with appropriate pipe glue or cement. After ensuring all connections are secure and leak-free using pressure testing methods such as filling up sections continuously with water while observing any leaks carefully - backfill excavated areas properly compact soil around newly installed pipes protect them potential damage caused by shifting ground movements future.
Installing Vent Pipes
The Imperative Role of Vent Pipes in Deterring Sewer Gases
One fundamental component of a comprehensive plumbing system that is often overlooked is the vent pipe. Vent pipes, while unobtrusive and seemingly insignificant, play an essential role in the efficiency and safety of your garage's plumbing system. Their chief function lies in their ability to prevent the intrusion of noxious sewer gases into your detached garage.
Sewer gases, as their name suggests, are by-products of waste decomposition within the sewer system. Not only do they carry an unpleasant odor, but they may also pose health risks when inhaled for prolonged periods.
Some common components of sewer gases include methane, ammonia and hydrogen sulfide; all notorious for causing headaches, dizziness or even more severe health implications with sustained exposure. Incidentally, these harmful gases would intrude your space unabated if not for vent pipes.
These ingenious pieces of tubing provide an exit route for such gases leading them safely out above the roofline where they disperse harmlessly into the atmosphere. Thusly ensuring a breathable ambiance within your garage.
Navigating The Installation Process: Ensuring Proper Vent Pipe Placement
In order to perform their intended function effectively, it is crucial that vent pipes are installed correctly. Their installation process involves a few systematic steps that require meticulous precision to ensure optimal functionality.
The first step involves strategically determining where to position your vent pipe connection. Ideally, this should be as close to the fixture trap as possible because this is typically where sewer gases tend to accumulate due to its curvature designed to hold water acting as a seal against such gases.
However, each fixture requires its own separate vent branch which should converge into a main stack leading up through and out above your roof. The next step includes measuring and cutting correct lengths of pipe and coupling them together using relevant fittings like tees or wyes wherever branching occurs.
PVC glue can be used on plastic pipes while soldering copper ones ensures secure connections void off leakages which could compromise their performance or cause water damage over time. The final step entails ensuring the top end of the vent stack protrudes high enough above your roofline (usually about two feet) so that escaping gasses cannot re-enter through windows or other openings and are instead safely diffused into open air away from people below hence maintaining innocuous surroundings within your detached garage space.
The Final Piece: Connections and Testing
You've come to the stage where all your diligent preparation pays off - connecting your fixtures and testing the whole setup. Starting with fixtures like sinks, faucets or toilets, ensure that the fixture has a shut-off valve. This will be crucial in controlling water flow directly at the fixture during future maintenance or emergencies.
Connecting your fixtures largely depends on the type of pipe you used for your plumbing system. If you've opted for PVC or CPVC pipes, you'll need to apply a primer and solvent cement before attaching a fitting.
PEX pipes require specialized expansion tools and fittings. Copper pipes involve soldering which requires heat application - take necessary precautions if this is your chosen route.
Once all fixtures are connected appropriately, it's time to test your plumbing system. Gradually open the shut-off valves and inspect for any obvious leaks at each connection point.
Allow water to run through all outlets; sink faucets should be opened fully and toilets flushed multiple times to ensure proper drainage. In this phase, vigilance is key - minor leaks can become major headaches if not addressed early.
Conclusion: Celebrating Small Victories
Running plumbing to a detached garage may seem like a daunting task, but with careful planning and execution it can certainly become an achievable feat even for less experienced DIY-ers. Remember that every pipe connected correctly is a small victory leading towards the ultimate goal of self-reliance in maintaining one's property. This process not only adds convenience but also value to your property while expanding your individual skill set - indeed something worth celebrating!